Impacto
de los proyectos del Instituto
El
Puente Chiapas
El
Gobierno Federal, a través de la Secretaría de
Comunicaciones y Transportes (SCT), está construyendo
el puente Chiapas, parte de un ambicioso programa carretero
por mucho tiempo esperado, para unir el estado de Chiapas con
el centro del país, con el cual se promoverá el
crecimiento económico y turístico de la región.
A
mediados de 1997, la Dirección General de Carreteras
Federales de la SCT inició los estudios de factibilidad
para proyectar un puente que cruzara la presa Nezahualcóyotl
o Malpaso. Los estudios incluyeron levantamientos topográficos
y batimétricos, estudios geotécnicos, socio-económicos
y de impacto ambiental, y análisis de aforos. Se evaluaron
varias propuestas incluyendo la de un puente atirantado y la
de un puente suspendido. Sin embargo, se eligió la de
una superestructura ortotrópica empujada con sección
transversal tipo cajón, que se apoyaría en pilas
o jackets del tipo de las plataformas marinas. El diseño
del puente se terminó a finales de 1999 y consistió
en una superestructura continua de ocho claros de 124, 168,
168,168, 168, 168, 152 y 92 m con una longitud total de 1 208
m. Los tramos de 168 m representan un record mundial en lo que
se refiere a la longitud de voladizo y al tipo de construcción
de puentes empujados.
En
2001, los ingenieros de la SCT encargados de la construcción
del puente realizaron una revisión del diseño
de la superestructura, y encontraron que algunos requisitos
prescritos para la construcción y el diseño del
puente no se cumplieron completamente en el diseño original.
Debido a la importancia de esta obra y a sus características
particulares, se propuso una revisión de la factibilidad
de su construcción y de su diseño original. A
finales de 2002, el IIUNAM fue elegido como el Consultor principal
para la construcción y empujado de la superestructura,
para la verificación del control de calidad de su fabricación
y para proponer el refuerzo de aquéllos elementos que
requirieran resistencia adicional; así como para monitorear
la seguridad estructural de la superestructura durante las diferentes
etapas de empujado.
Fabricación
de la superestructura
La sección transversal de la superestructura es un cajón
ortotrópico de acero de 5.50 m de altura (fig 1), rigidizado
con bulbos longitudinales que se colocan en el patín
(piso) inferior y superior. El patín o piso superior
tiene un ancho de 10 m y alojará dos carriles de circulación.
Fig
1 Diferentes partes o subensambles de una dovela de sección
cajón
Originalmente,
la fabricación de las diferentes partes de un segmento
o dovela se realizaron en un taller cercano a Toluca. Desde
este taller se transportaban al sitio de la obra (aproximadamente
a
1 000 km), donde se ensamblaban mediante soldadura de filete,
de penetración parcial o de penetración completa,
para conformar una dovela de 12 m de longitud. Una de las labores
permanente y constante del Instituto de Ingeniería, consistió
en revisar y realizar inspecciones no destructivas (ultrasonido,
partículas magnéticas, radiografía) de
las soldaduras. Con estas pruebas se verifica que las soldaduras
se apliquen y cumplan con los requisitos establecidos en los
reglamentos de construcción de este tipo de estructuras.
Los segmentos o dovelas se unen hasta lograr una longitud adecuada
de lanzamiento. En otras palabras, se verifica la calidad de
la fabricación de las dovelas.
Después
de una revisión del proceso de fabricación original
y de la construcción de las primeras 28 dovelas, se decidió
fabricar y transportar las 12 piezas de las dovelas en dos partes
o úes, una superior y una inferior (fig. 2). Actualmente,
sólo estas dos partes y los bulbos de continuidad se
sueldan en la obra, mientras que el taller de fabricación
se habilitó en Tuxtla Gutiérrez, Chiapas, aproximadamente
a 80 km del sitio de la obra. El número total de dovelas
fabricadas en Tuxtla Gutiérrez fue de 74.
Figura
2.- Transporte de una “U” inferior
En
el sitio se realizó una excavación de 320 m de
longitud detrás de uno de los apoyos extremos (fig. 3).
De acuerdo con el ciclo de empujado, varias dovelas o segmentos
se alínean dentro de esta excavación y se fijan
al último segmento del ciclo anterior de empujado. Dentro
del cajón se encuentran dos vigas de concreto presforzado
en las cuales se colocan unos apoyos rodantes temporales sobre
los cuales se desliza la superestructura durante el empujado.
Una vez que la superestructura sale de esta excavación,
se convierte en una estructura en voladizo, hasta que llega
a una de las pilas ya construidas en la presa.
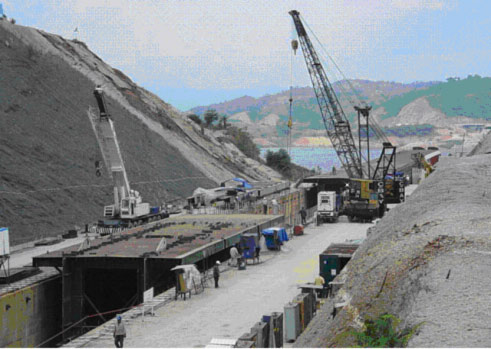
Fig
3 Patio de ensamble y empujado de las dovelas de sección
cajón
Empujado de la superestructura
Una vez ensamblada, la superestructura es empujada utilizando
en la punta una estructura ligera o nariz de lanzamiento de
44 m de longitud y 120 t de peso. Para reducir el nivel de esfuerzos
a lo largo del tablero y controlar las deflexiones verticales
de la punta de nariz de lanzamiento, se utiliza un mástil
provisional con tirantes, de forma que durante el empujado se
conforma un puente atirantado (fig 4). Tal como se mencionó,
hasta la fecha, la longitud de 168 m de cinco de los claros
del puente será la más larga construida en el
mundo utilizando este sistema (empujado por incrementos sucesivos).
Para tener una idea de la magnitud de la obra, se puede comparar
con el distribuidor vial recién construido en el DF.
El claro de mayor longitud del puente Chiapas es aproximadamente
cinco veces más grande que el mayor claro del distribuidor
vial; la altura máxima de las pilas del puente Chiapas
es aproximadamente tres veces más alto que la mayor de
dicho distribuidor. Una dovela o segmento de 12 m de longitud
del puente Chiapas pesa en promedio 95 t, mientras que el peso
de una de las trabes “ballena” del distribuidor
es de 100 t.
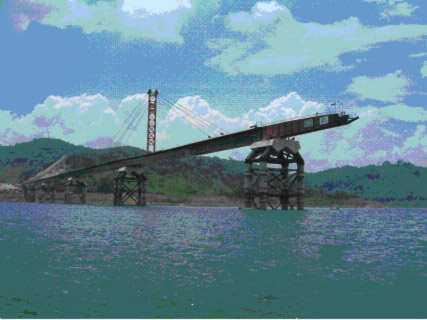
Fig
4 Vista general del Puente después del 5º empujado.
Se observa el mástil con los tirantes y la nariz de lanzamiento
El
empujado se dividió en ocho ciclos o etapas, cada una
de las cuales se logró gracias a dos gatos hidráulicos
horizontales colocados entre cuatro mordazas en la parte posterior,
o última dovela del ciclo de empujado. Según el
movimiento del gato, dos mordazas se aprietan o fijan contra
las dos trabes de concreto presforzado, mientras que las otras
dos mordazas se mueven con la superestructura; dos de las mordazas
siempre van sujetas con unos elementos de acero a la última
dovela del ciclo de empujado. Las dovelas que no forman parte
del voladizo se deslizan sobre unos apoyos rodantes colocados
sobre una pista de acero inoxidable, la cual está fija
a las mismas trabes.
Al
empujar la superestructura, las dovelas de vanguardia vuelan
una cierta longitud, dependiendo del claro por salvar. Este
voladizo tiene una deflexión vertical en la punta de
la nariz de lanzamiento, que no coincide con el nivel de empujado
en las pilas, por lo que antes del arribo de las dovelas de
vanguardia a la pila correspondiente, se tiene que realizar
una delicada labor de recuperación de esta deflexión.
Una
vez que las dovelas de vanguardia se montan sobre la pila correspondiente,
éstas se deslizan, en sincronía con las dovelas
de retaguardia, sobre apoyos móviles colocados también
en pistas de acero inoxidable de 4 m de longitud. Después
de cada ciclo de 4 m se utilizan gatos hidráulicos para
levantar las dovelas y que regrese el apoyo móvil.
El
Instituto de Ingeniería participa también en la
coordinación de maniobras tanto en tierra firme como
en cada una de las siete pilas del puente.
Modelación
por computadora
En el IIUNAM se elaboró un modelo tridimensional de elementos
finitos para revisar el diseño original y verificar los
esfuerzos durante el proceso de empujado (fig 5). Además
de ser útiles para verificar la respuesta global del
tablero, estos modelos son buenos para evaluar concentraciones
de esfuerzos, un aspecto no considerado completamente en el
diseño original. Se utilizaron elementos cascarón
para modelar el tablero –incluyendo las almas, patines,
bulbos, diafragmas y atiesadores– y vigas tridimensionales
solo para modelar el mástil, los tirantes y contraventeos
de la nariz de lanzamiento.

Fig
5 Vista isométrica del modelo tridimensional
Gracias
al modelo matemático desarrollado en el Instituto, se
pudieron considerar desalineamientos, faltas de planeidad, así
como otros problemas de tolerancias dimensionales que surgieron
durante la aplicación de soldadura y ensamble de las
dovelas. En el IIUNAM se evaluó la influencia de estas
variables en el comportamiento de la superestructura; además,
se realizaron análisis de sensibilidad para evaluar la
influencia de omisiones en el diseño original y errores
en la construcción. En algunas zonas de la superestructura,
principalmente en las primeras dovelas, los resultados del análisis
estructural del modelo revelaron un problema de fatiga a corto
plazo, relacionado con los momentos flexionantes temporales,
positivos y negativos, y las altas fuerzas cortantes que ocurren
durante el empujado.
Con
base en los resultados obtenidos, se propusieron refuerzos a
la superestructura para soportar las concentraciones de esfuerzos
originadas durante el empujado. También se predijo la
aparición de algunos pandeos de las almas que se observaron
en el segundo y tercer ciclo de empujado, y se colocaron elementos
estructurales adicionales para corregir las distorsiones y desalineamientos,
además de aplicar algunas medidas correctivas adicionales.
Instrumentación
Personal del IIUNAM diseñó un sistema de instrumentación
para complementar los resultados del modelo matemático
y para preservar la integridad estructural de la superestructura.
El sistema se puede configurar en cualquier intervalo y umbral
de registro, y también permite el procesamiento gráfico
de las historias de deformaciones y temperaturas (fig 7).
El
sistema de monitoreo incluye deformímetros, anemómetros,
DCDT, sensores de temperatura y de aceleración. Todos
se conectan, a través de amplificadores, filtros y acondicionadores
de señal, a una computadora personal donde se registran
las mediciones, la cual se localizaba en la última dovela
del empujado y permitía el monitoreo en línea
de los registros; también se lleva un extensivo registro
topográfico de cada ciclo de empujado. Hasta la fecha,
el sistema ha trabajado satisfactoriamente en las primeras seis
etapas de empujado.
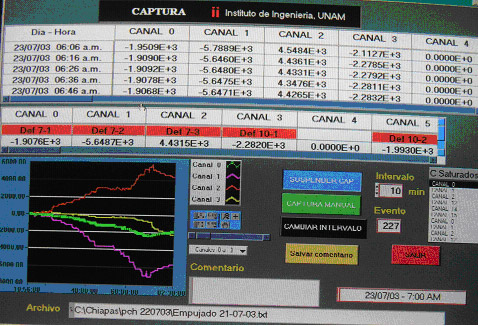
(a)
(b)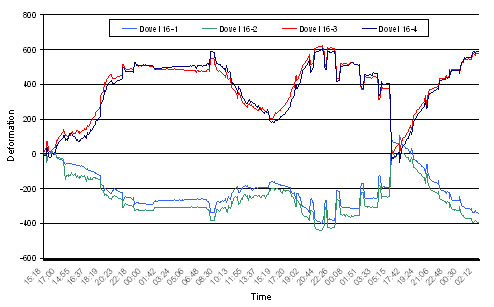
Fig
6 (a) Pantalla de la computadora de registro, y (b) ejemplo
de una historia de deformaciones registrada
Comentarios
finales
La etapa final de empujado está programada para fines
de noviembre, mientras que el asfalto, parapeto y obras complementarias
se terminarán los primeros días de diciembre.
Tentativamente, la inauguración oficial del puente se
hará el 24 de diciembre, lo que representa un regalo
extraordinario de Navidad para Chiapas.
Este
proyecto es realizado por un grupo interdisciplinario integrado
por los investigadores Roberto Gómez Martínez,
David Muriá Vila, José A Escobar Sánchez,
Roberto Sánchez Ramírez, M Ángel Mendoza
García, Gerardo Rodríguez, David Muñoz
Vizuet, Ricardo Vera Ramírez, Ponciano Trinidad López,
y más de 20 técnicos y becarios de la Subdirección
de Estructuras y Materiales.